How to select the perfect AMR in 4 steps
You want to automate your intralogistics and enter “AGV” or “AMR” into your search engine. The results are almost endless. You see a variety of different robots, from under riders to extremely large pallet trucks and everything in between. So where to begin?
1. Analyse the current situation
You can’t decide on the perfect AMR if you don’t have a clear understanding of your processes. There is no such thing as the perfect AMR, there is only the perfect AMR for you. So the first step is to get a clear understanding of the current situation in your company.
What is the environment of the AMR?
Do you want an AMR to transport medicines in a hospital or do you want to move paper rolls throughout a factory? Will the AMR drive amongst people or in restricted areas? Do you need the AMR to drive outdoors or only indoors? And most AMRs don’t like ramps and large joints in the floor.
What is the payload?
Obviously there is a difference between an AMR that can transport paper rolls of 4 tons than an AMR that transports boxes with medicines throughout a hospital. You can make your search more specific by looking for “pallet AMR” or “small load carriers amr”.
What are the processes?
Make an analysis of all internal goods movements. This gives an idea of all the possible processes that are eligible for automation.
TIP: to increase the ROI of your project it could be beneficial to have a wider scope, because sometimes a process prior to or after the process could be automated as well.
Communication protocols?
Does the AMR need to communicate with hardware devices like doors, elevators, machines or safety systems?
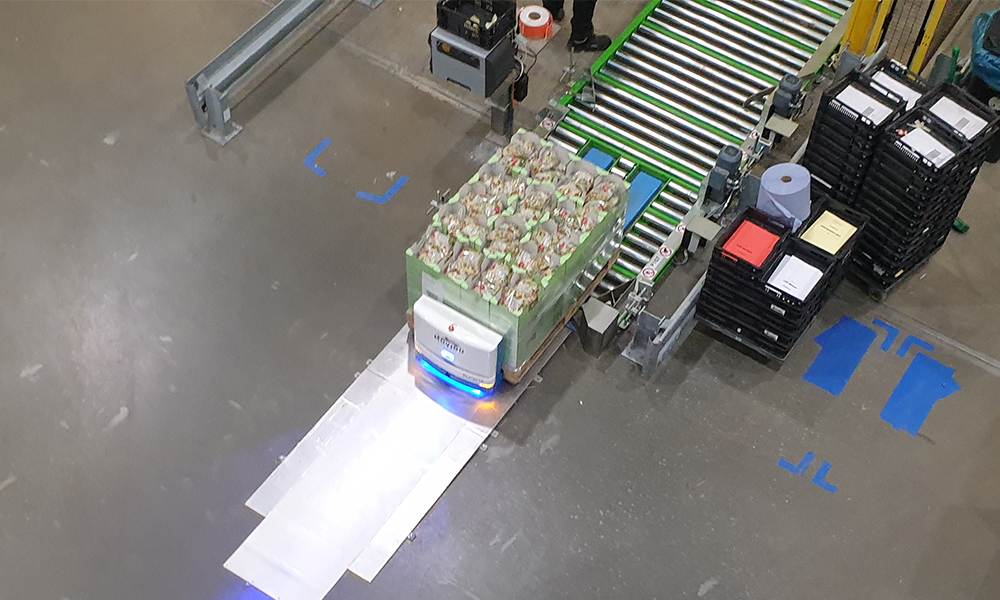
Based on the information gathered, you have a good idea of the scope of your project and what the AMR should be capable of. Often the project is too large to do at once, so it is advised to split the project into different phases. How to select the (part of the) process to start with?
2. Where is the money?
Intralogistics is waste according to the lean philosophy, so should be eliminated when possible. In the first step you listed all the movements, now we elaborate on that list, because it is important to see where the money is. Who is handling the internal transports and how often do they take place?
Who is handling the internal transport?
Are there dedicated people responsible for the internal transport of goods? Or are the machine operators taking pallets to the next station, resulting in downtime of their production line for the time they are away? We have seen cases where production capacity increased by 40% when transport was automated and operators could remain at their station.
How much time does it take?
Get insight into how much time it takes to handle all the transports. The best way to do this is by just hands-on: take a stop-watch and measure. Theoretically it can take, for example, 1 minute to transport a pallet from production to finishing. But in practice we see that the person doing the transport sees his co-worker at finishing and has a small chat. This increases time drastically and shouldn’t be overlooked.
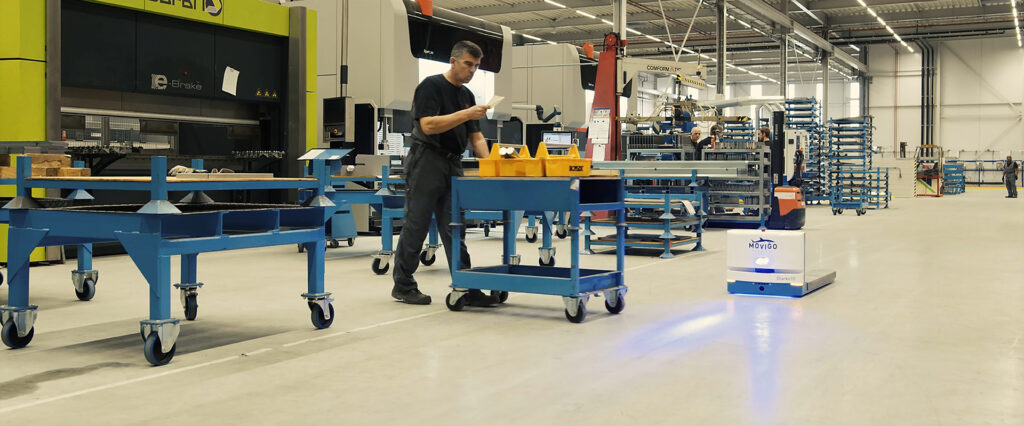
Automating everything at once is normally not the best strategy. It is better to divide the project into phases. With the information you are able to determine which processes are the most cost effective to start with. Start with the low-hanging fruit, because it is the best way to get quick ROI and a first success for your automation project.
3. Scan the market for AMRs
Now you have a clear idea of the project and requirements, you can start looking for potential suppliers. There are multiple ways to start your search. A Search engine on the internet is the most often used way. Because you already have an idea of the project scope, you can enter more specific keywords, like “Pallet AMR Production” or “hospital agv”. Another way is via comparison sites like LotsofBots or ANTDriven. Make a shortlist of vehicles that meet your requirements with regards to payload, safety, environment and other.
4. Decide the AMR that has the best fit
Now you have a clear idea of the project and requirements, you can start looking for potential suppliers. There are multiple ways to start your search. A search engine on the internet is the most often used way. Because you already have an idea of the project scope, you can enter more specific keywords, like “Pallet AMR Production” or “hospital agv”. Another way is via comparison sites like LotsofBots or ANTDriven. Make a shortlist of vehicles that meet your requirements with regards to payload, safety, environment and other.
Then the most important part: selecting the AMR that has the best fit for the processes you want to automate. The robot has to adapt to your process and not the other way around. Flexibility and adaptability are more related to the competences of a supplier than specifications of an AMR, so get in contact with a few suppliers and try to find out how flexible and adaptable they are. You need software engineers and process specialists to adapt the solution to your needs. So if suppliers advise you to change your environment or inform you that their robot still requires manual input, for example to manage locations or because the robot can’t communicate with hardware? Then there might be other suppliers that offer a more suitable alternative.
Conclusion: there is no such thing as the perfect AMR. There is only the perfect AMR for your process. So use the steps to get a clear idea of the process you want to automate and discover which supplier can provide a solution adapted to your process.